Last Updated on July 1, 2024 by
While Chendamangalam saree is globally famous, it is interesting to know its production process and why Chendamangalam Handloom deserves a visit while in Kochi, Kerala.
If you are an art and culture enthusiast, Chendamangalam is definitely your calling. This is a village where most locals are involved in handloom processing for decades. As Chendamangalam is considered to be a place that produces some of the best quality handlooms in Kerala, it is called – The Handloom Village. It is also one of the best places to visit near Cherai Beach.
Light rains welcomed us in Chendamangalam. 2 shops in front of a humble 1-storey building confused us as to where to go exactly. We saw a few people at the back of the building and decided to follow them.
It was a group of design students who has come to understand the process of Chendamangalam handlooms. We joined the group and Dr May Jacob, Research Director, Chendamangalam Handlooms Viability Project (CHELA) welcomed us all and gave us the following information. All the details in the blog are written after a discussion and demonstration by her.
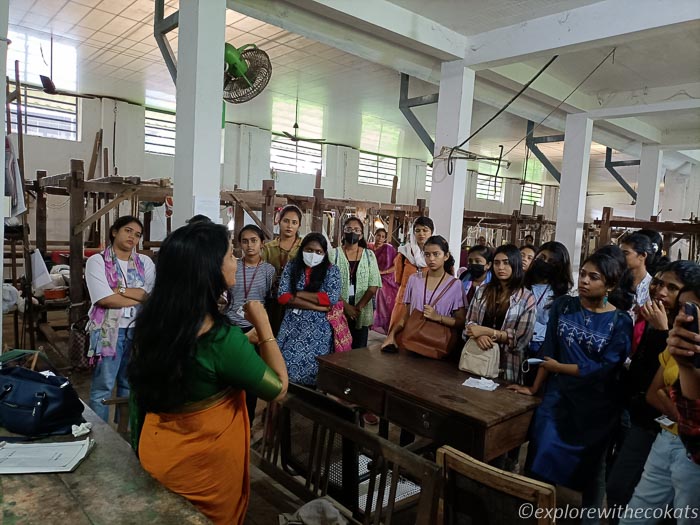
Table of Contents
About Chendamangalam
Chendamangalam is a village located 30 km away from Ernakulam town and is blessed with artisans who are skilled at the traditional craft of handlooms. Chendamangalam is nestled on the banks of three rivers and was part of the ancient port complex of Muziris. It is known for its fine cotton spun here by a community of weavers originally from Karnataka known as Devanga Chettiars.
Handlooms in Kerala
There was a golden period for Handlooms in Kerala and handlooms have existed here since 851 CE. This has been recorded by an Arab trader called Suleiman who said that Kerala had a fabric as thin as air and it was exported from the Muziris port to Gulf countries. This is mentioned in the book ‘A Frayed History- The Journey of Cotton in India’ by Meena Menon and Uzramma.
In order to cater to the demand for the fabric in the Gulf countries, many cotton weaving clusters were developed in Kerala. The weavers who migrated to Kerala for this demand were actually from Saurashtra in Gujarat and the history of handloom in India is based on the concept of migration.
Other weaving clusters in Kerala are Kasaragod, Kannur, Balaramapur, Thrissur-Palakkad.
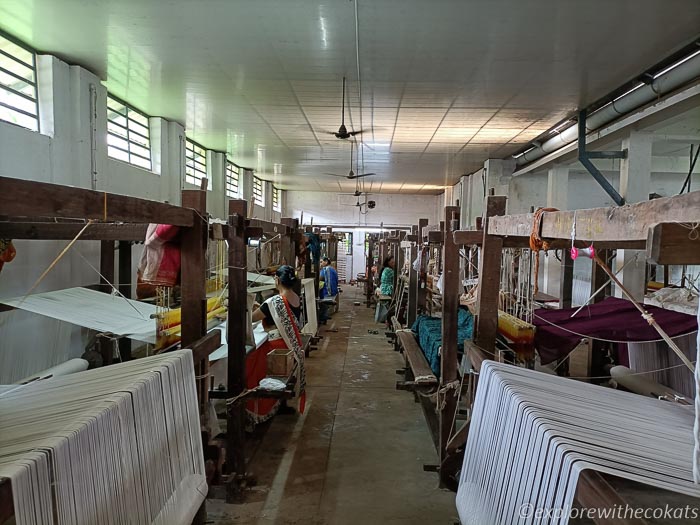
The History of Chendamangalam
Chendamangalam weaving cluster has had an intimate connection to the Paliam Palace, where Palian Achan lived. Palian Achan (elder minister) to the Cochin King lived in the Paliam Palace. Palian Achan needed new clothes every day before he went to the temple for prayers.
So the weavers of Chendamanagalam would weave new fabric for the Achan every day. He could not wear the off-white fabric every day (the traditional handloom cotton cloth with gold-threaded borders that originated in Kerala). So it had to be dyed with natural herbs.
Initially, clothes brought from Tamil Nadu were used by the Achan. But a trader from Chaliyan lineage presented the finest quality fabric to the king. The king was satisfied with this cloth and asked the trader to produce the same fabric in the village of Chendamangalam. This marked the beginning of handlooms in Chendamangalam.
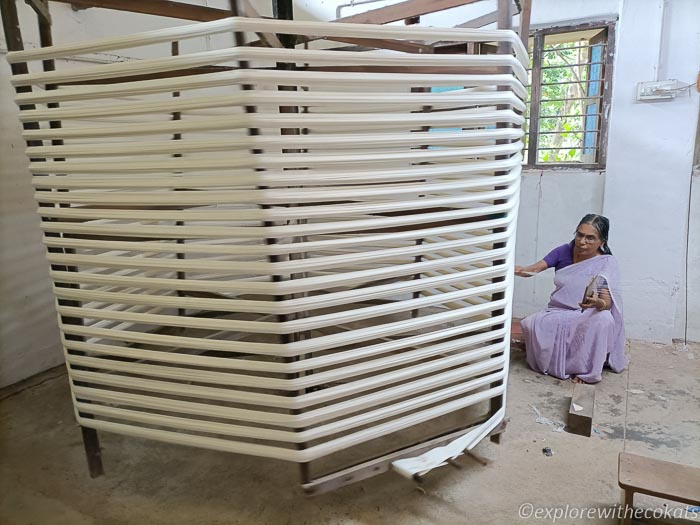
The Production of fabric in Chendamangalam Handloom
There are two types of handloom industry in Kerala:
- Co-operative based: meaning anyone can become a weaver
- Community-based: meaning the craft is restricted to the community members
In Chendamangalam, it is a communal and co-operative based enterprise. And there are 87% women weaves and allied workers in the Chendamangalam cluster.
The cotton fabric is painstakingly made in Chendamangalam. This production process is the testimony to it.
- The cotton yarn is received from the National Handloom Development Cooperation at a subsidized rate for the Chendamangalam handloom co-operative industry. The yarn is then given to the weaver.
- The weaver soaks the yarn in water for 7 days. Every day the yarn is taken out and stamped on by their feet and washed before soaking again. This is done to wash away any impurities present in the yarn.
- After 7 days the yarn is dried and then the spinning process begins on a hand-spun charkha.
- After spinning, the thread goes through the process of warp and weft wherein it is tied in a field and dried on streets.
- In order to make the fabric easy to dye, stiff and wrinkle-free, starch is added to the fabric. The natural starch used here is rice flour (so the fabrics are literally gluten-free!), coconut oil and water. The fabric actually has a faint fragrance of coconut oil. With each wash, this starch is washed away and that makes the fabric softer.
- After starching, the thread is dried again. The sun-dry process is very specific and is done before the sun is too harsh which is between 6 am to 8 am.
- Before the sized warp is loaded onto the loom, the yarn is aligned and separated to facilitate smooth weaving. The aligned and starched yarn is carefully wound around a wooden beam and carried to the loom.
- After joining the threads they are then loaded onto the handloom to start the weaving process.
Chendamangalam sarees and fabrics are made with fine-count thread and are renowned for the same. The usual yarn has a thread count of 120, 100 and 80. While the ones used here are of the count 2/120.
The entire process of making a saree from the yarn takes about 2 weeks. However, it all depends on the design of the fabric.
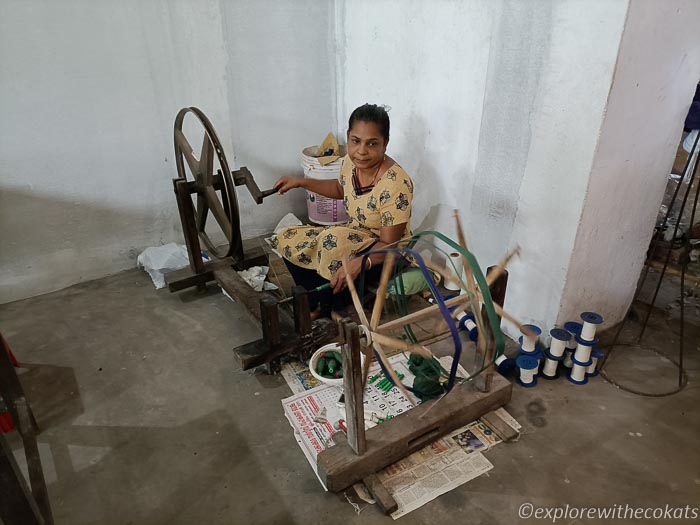
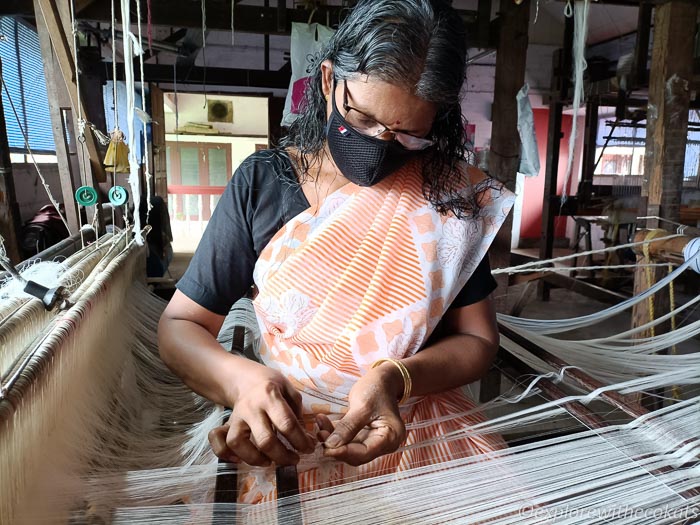
Why is the Chendamangalam saree so popular?
A Chendamangalam saree is recognisable by its puliyilakara (tamarind leaf border) border, a thin black line that runs abreast with the saree’s selvedge. The Government of Kerala applied for Geographical Indication (GI tag) for Chendamangalam sarees and it officially received a GI tag in 2011.
Chendamangalam Handloom and Sustainability go hand-in-hand
The handloom industry is recognized as an environmentally sustainable industry. Chendamangalam handlooms are especially sustainable because –
Did you know? Handloom complies with Sustainable Development Goals.
- It utilizes lesser fabric and lesser water to make one saree than a t-shirt. Handlooms for a sustainable future? Yes, please.
- One handloom employs 5 people – one weaver and 4 allied workers. Hence it supports an entire rural community.
- They use azo dyes and vat dyeing process which is relatively safe for the environment and the allied workers.
- A low power-intensive process so it saves electricity.
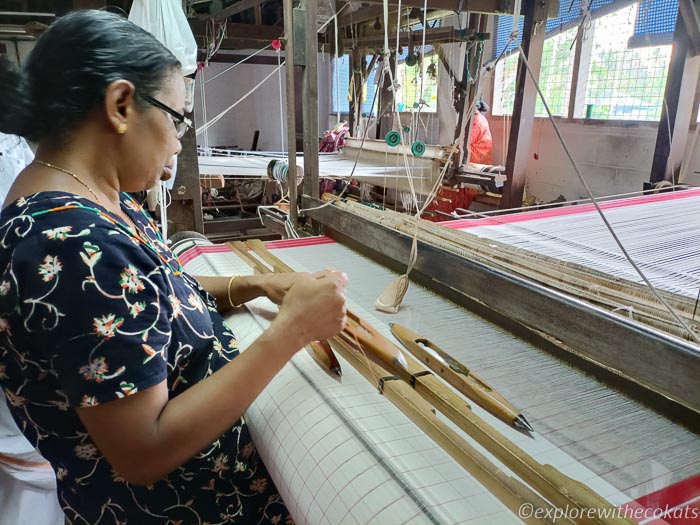
2018 Kerala floods and Chekkutty Dolls
The 2018 Kerala floods wreaked havoc on the entire state of Kerala. But since the village is situated on the banks of 3 rivers, this village was especially affected.
The floods destroyed the homes and handlooms equipment of Chendamangalam villagers. The raw materials and finished good worth INR 21 lakhs were damaged.
Gopinath Parayil and Lakshmi Menon came up with the idea of making dolls from the fabrics that were damaged. These dolls were called Chekkutty (short for “Cherine Athijeevicha Kutty”). Various NGOs, students and hundreds of volunteers joined the team and made thousands of Chekkutty dolls. This helped the locals of Chendamangalam for some financial independence after the floods.
Handloom Future?
- Dignified creative labour: A handloom school is about to be set up in Chendamangalam so as to encourage youngsters to continue this craft. To make them realize that weaving is important as designing and that weaving is a profitable business.
- NABARD and Chendamangalam Weavers came together and formed a Consortium during the pandemic as the weavers could not be given wages due to no sales even during festivals. They have formed an online platform called Coop Loom where people can buy handloom from the e-commerce website.
- Handlooms in India lack sales and marketing. Youngsters should realise the importance of handlooms and that the locals are dependent on this dying art. Unless we support them, the younger weaver generation would not want to take this up.
- A craft tourism trail is being set up in Chendamangalam for students and tourists so that the relevance of handlooms is known to all.
Read More Posts on Handicrafts of India
Gujarat: Crafts of Kutch
West Bengal: Sabai Grass Handicrafts
Rajasthan: Jaipur Blue Pottery
Read More Kerala Posts
- Kerala Backwaters of Alleppey
- Human by Nature: Impressions from Kerala
- Places to visit in Thekkady
- Responsible Tourism in Kumarakom, Kerala
- Kerala road trip guide
- Periyar National Park
- Glamping in Munnar, Kerala
- Things to do in Thiruvananthapuram
Disclaimer – This post contains affiliate links. It means it adds no extra cost to you if you book through the link but I get a referral bonus which helps me earn a little to keep this website up and running.
Pin this post!
